Headquartered in Tokyo, Japan’s supplier organisation, JAPIA (Japan Auto Parts Industry Association) is rapidly assessing the impact of the recent catastrophic explosion at Nylon 12 resin producer, Evonik’s factory in Germany.
JAPIA executive managing director Takehide Takahashi spoke to Simon Warburton from Tokyo about how the association was addressing the situation and what impact it could have on Japan’s supply chain, despite what appears to be difficulty in obtaining information about the lack of PA12.
j-a: How is Japan coping with the shortage of Nylon 12 – Evonik is estimating an October restart at the earliest?
TT: “We must be practical – if so many people want the same PA12 then the shortage is a quite visible danger – so we have to change the PA12 to other material.
“Practical activity may need to be necessary – if this shortage lasts for long – [to] this October or next March. I am not a crystal gazer – if you see a long time to recover you have to change and do something quite practical.”
j-a: Have you experienced anything similar to the German explosion in Japan?
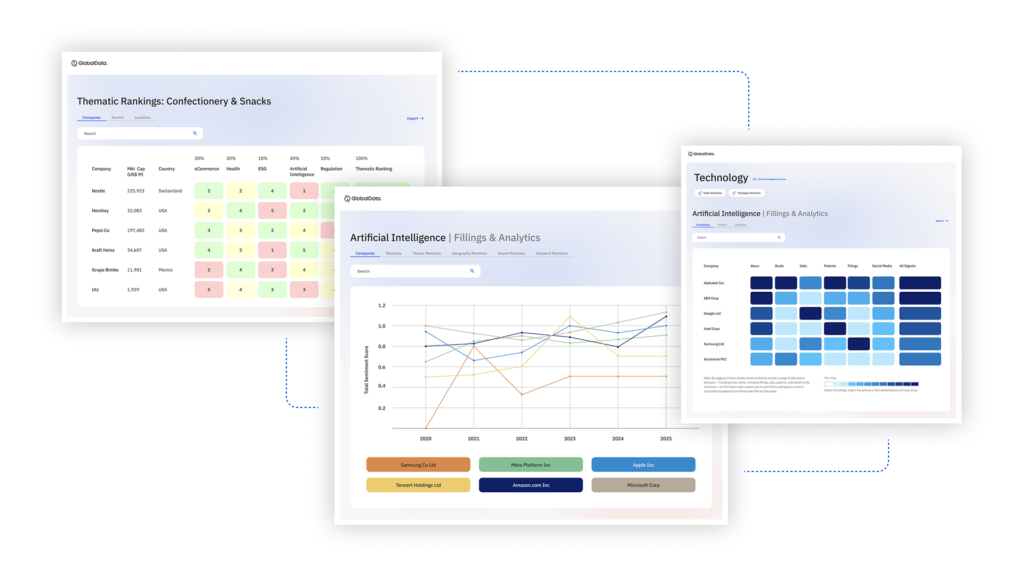
US Tariffs are shifting - will you react or anticipate?
Don’t let policy changes catch you off guard. Stay proactive with real-time data and expert analysis.
By GlobalDataTT: “A very big accident happened in Japan with a similar chemical plant – it was a couple of weeks ago [in] Iwakuni – an American forces base.
j-a: The US Original Equipment Suppliers Association (OESA) recently met together with the Automotive Industry Action Group in Michigan to discuss the chronic lack of Nylon 12 – what is JAPIA doing?
TT: “We are still in touch with them [OESA, CLEPA] because PA12 is a growing concern even for Japanese companies.
“I ask my colleagues to get information on PA12 – unfortunately there is not so much information on that
j-a: Does Japan produce any of its own Nylon 12?
“I heard several [Japanese] chemical companies produce PA12 or [a] similar kind. So they may produce PA12 if there are no intellectual property problems and [if] the capacity of the facilities is available. The PA12 producer [s] are here in Japan and they are healthy.”
“When you see the networks between the part-makers, you can do something and we have been doing something to avoid the unfortunate situation.
“Concerning the raw material companies, it is very difficult to understand each other and who is making what. The lack of information is quite huge. You can’t get every information because the situation is changing – only fragments you can have – you have to guess.
j-a: Can you gauge the impact of the Nylon 12 shortage on Japanese automakers?
TT: “The atmosphere of our industry – PA12 is not so severe for them – I am judging from what they are saying to me. Nobody is screaming: ‘PA12 is choking me.'”
j-a: When do you envisage Nylon 12 supply returning to normal?
TT: “Unfortunately, I have no idea on it.”
j-a: Can you envisage supply-chain problems later on due to the shortage?
TT: As I’m not a crystal gazer, I can’t give you any ideas on supply chain problem. For Japanese companies, magnitude of Nylon 12 problem is different if their manufacturing sites are operating overseas or domestic.
j-a: Given your experience of the tsunami last year, can you offer any advice to those affected by the shortages to find interim solutions?
TT: “Do your best for finding dead stock through supply network, equivalent substitutions and speeding up the process of adopting substitutes and so on.
“In short, be practical.”