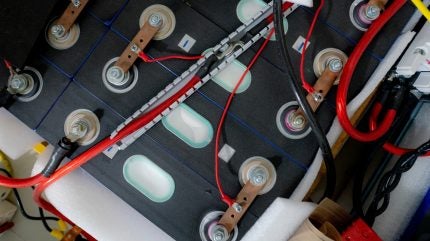
In the automotive sector, Scope 3 emissions make up 99% of total value chain emissions. The majority of these Scope 3 emissions occur upstream through the extraction of raw materials and the manufacturing of components. For most businesses, they are the most challenging to calculate.
With increasing pressure from consumers and governments worldwide to reduce emissions, OEMs are ramping up electric vehicle (EV) production, with battery electric vehicles and hybrids accounting for half of all light vehicle sales by 2027, according to GlobalData.
The electrification of the industry will play a critical role in decarbonisation efforts. With all OEMs intending to increase their EV and hybrid offerings within the next decade, investment in battery and EV production plants has surged globally. As such, many OEMs are developing partnerships with battery suppliers to gain a competitive advantage in battery technology.
However, while electrification will significantly reduce the automotive industry’s Scope 3 GHG emissions, one of the biggest drawbacks of producing EVs is the environmental impact of sourcing and manufacturing of these batteries, making recycling battery cells and the implementation of a circular economy a crucial step towards sustainability.
We spoke with Roy Housh, commercial director at Frewitt, a leading industrial equipment supplier headquartered in Switzerland, on the crucial role of battery recycling in the EV industry’s circular economy.
Can you briefly explain the current state of EV battery recycling and its importance in the transition to electric vehicles?
Roy Housh: The principal raw materials in the EV batteries are very finite, notably copper, nickel, lithium, cobalt, manganese, as well as battery-grade graphite. All these materials are costly to mine and come with significant environmental and human impacts.
What are the main challenges currently facing the EV battery recycling industry?
RH: One of the main challenges in the EV battery recycling industry is the current lack of economic and regulatory incentives to encourage and channel actors towards the recycling of fuel cells with complex chemistries and constructions. Very often, recycling processes have been placed together piecemeal, and therefore, the different steps of recycling lack efficiency and user-friendliness.
What are your thoughts on the circular battery economy, and how do you see it evolving in the next decade?
RH: Current trends show that countries and companies are becoming far more circumspect when it comes to being dependent on raw material sources from other countries and continents where they are unable to apply influence. Recycling will not always be relegated to being the ‘Plan B’. It will become a Good Business Practice and a National Security Priority.
What changes would you like to see in battery recycling legislation?
RH: Recycling should be done where the batteries are consumed, and not off-shored. Off-shoring defeats the purpose of removing/avoiding dependence.
How do Frewitt’s recycling processes differ from traditional methods?
RH: Frewitt has over four generations of experience in size-reducing and handling bulk solids, including very dangerous materials, such as cytotoxics. We have used this expertise to create turn-key solutions that allow recycling, from the shredding or crushing of fuel cells and the segregation of the metals from black mass, to screening, de-agglomeration, and/or micronisation. By combining these steps on one contained platform, Frewitt prepares the black mass, reaching the required particle size distribution, which will allow the recycler to dissolve the black mass in a hydrometallurgical process using acids and recover the valuable metals.
What innovations are you implementing to make them more sustainable?
RH: Frewitt is incorporating a patented milling-under-vacuum process for numerous products that are either dangerous if inhaled, potentially combustible, or heat sensitive. Frewitt has also developed its patented PMV-320 Pin Mill – the highest mechanical energy pin mill on the planet, which can also work under vacuum and reach very fine particle size reductions that were previously reserved for jet mills only. Because we use our patented vacuum process, the process makes no noise.
What role do you see new battery chemistries playing in the future of recycling?
RH: There are a lot of expectations from lithium-sulphur batteries. The Li-S batteries would be lightweight, with sulphur in the positive electrode and lithium as the negative electrode, theoretically being far denser in energy than current batteries. The processing of sulphur will play well to Frewitt’s strengths of containing materials and the milling of irritant and potentially dangerous material.
What do you think EV battery recycling will look like in five to 10 years?
RH: Hopefully, it will be optimised to the point that the need for new raw materials in order to sustain the industry will be minimal.