
With the Renault Emblème demonstrator car, the Renault Group recently presented its vision by 2035 of a low-carbon family vehicle. Through Emblème, Renault says it is continuing the exploratory studies initiated with the Scenic Vision concept in 2022.
The car embodies a number of innovations in sustainable tech, working with key suppliers, that Renault envisages are a pointer to current and future applications when the cost and production economics allow.
Renault maintains that transitioning from a combustion model to a 100% electric model is equivalent to reducing its CO2 emissions by around 50%. Moreover, Renault Group already incorporates an average of 30% of materials from the circular economy in its new models.
Renault’s approach is to address the entire vehicle life cycle from cradle to grave in five key areas: eco-design, selection of resources, production, use and end of life.
Developed by Ampere (Renault’s electric tech unit), Renault Emblème is a demo car reflecting this approach. A vision of a low-carbon family car from start to finish, Renault says it emits 90% fewer greenhouse gases (CO2eq) over its entire life cycle than the 2019 baseline. Renault says it embodies an innovative laboratory for the future generations of Renault brand’s vehicles.
By involving a range of industrial partners in the eco-design process, Renault says it has been able to optimise the choice and diversity of materials used for Renault Emblème from the outset. The list of partners included: AKWEL, Autoneum, ArcelorMittal, CEA (French Alternative Energies and Atomic Energy Commission), Constellium, Dicastal, Forvia, Forvia / Hella, Michelin, OPmobility, STMicroelectronics, Valeo and Verkor.
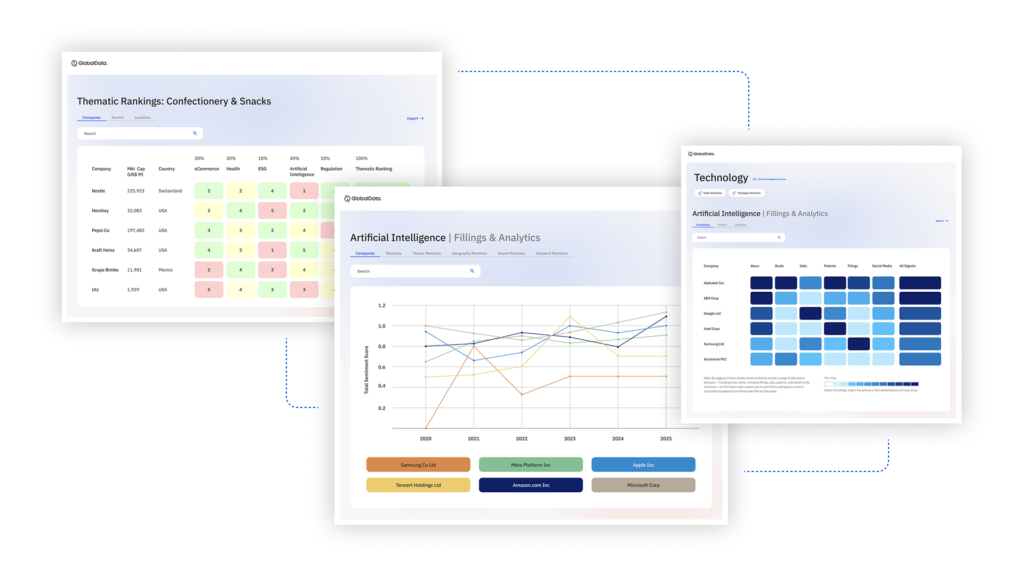
US Tariffs are shifting - will you react or anticipate?
Don’t let policy changes catch you off guard. Stay proactive with real-time data and expert analysis.
By GlobalDataStringent specifications set out every detail of the vehicle’s composition in order to achieve a 70% reduction in the carbon footprint of parts production: steel, aluminium, plastics, tyres, glass, electronics and so on.
More than twenty partners worked on the project with Renault and Ampere. To achieve the highest possible level of decarbonisation, each partner implemented their own innovations at their own level in pursuit of the most appropriate energy efficiency solutions involving the use of low-carbon energy as part of a circular economy approach.
Door handles – AKWEL
The “sensitive” door handles were designed under an eco-design approach. Extremely favourable for aerodynamics, their optimised design has reduced the overall weight of the finished part by 60%. Renault says the simplification of the mechanism has resulted in a reduction of 50 components, while still providing an opening activation response of 0.1 seconds.
The parts, made from a single material, contain 65% recycled content, contributing to an 88% reduction in carbon emissions.
AKWEL also designed the electric hood opening system for the front trunk “Frunk”.
Body parts – ArcelorMittal
Using advanced high strength steels (AHSS) and press hardenable steels (PHS), ArcelorMittal reduced the weight of the steel required for the body-in-white by 8%, for greater energy efficiency and decarbonisation. The XCarb Recycled and Renewably Produced steels in the B-pillar include a high level of circular content (minimum 75%) and are produced solely with renewable electricity, for a 69% reduction in CO₂eq. emissions. ArcelorMittal aims to achieve carbon neutrality by 2050, through a combination of technologies that may include direct iron reduction, the use of natural gas and green hydrogen.
Single-material thermal and acoustic insulation – Autoneum
Autoneum designed 32 parts for Emblème with thermal and/or acoustic properties, both inside and outside the vehicle. They include the underbody fairing, floor mats, boot liners, acoustic parts, powertrain compartment absorbers and front storage. These parts were made from single-material polyester fibres, which are extremely light and easy to recycle. The production process made maximum use of renewable electricity and recycled off-cuts. Based on weight savings (25%), a high level of recycled content, a waste-free production process and the excellent recyclability of end-of-life materials, Autoneum was able to reduce the overall carbon footprint of its components by 70%.
Aluminium doors – Constellium
One key advantage of aluminium is that it can be recycled infinitely without losing any of its properties. Processing recycled aluminium for body panels requires just 5% of the energy needed to produce primary metal.
To make the doors for Emblème, Constellium used primary aluminium, produced by electrolysis using low-carbon electricity, and recycled aluminium from the circular economy. This illustrates the long-term circularity potential of aluminium in cars.
Alloy wheels – Dicastal
The Renault Emblem rims have been designed with eco-design in mind, with a design close to the solid wheel, particularly conducive to aerodynamics. Thin and extremely light (wheel 16.5kg and addon 0.88kg), they are made from aluminium of 70% from the circular economy.
Interior – Forvia
For the vehicle interior, particularly the dashboard, Forvia selected coverings based on recycled or natural materials (linen, pineapple), which also have the advantage of being carbon sinks, i.e. capable of storing CO2.
The contact zones on the door panels and central console are upholstered in skins made from pineapple fibres, described as a lighter and more sustainable alternative to animal leather.
The dashboard is upholstered in linen made in Normandy (France). This innovative process adds structural properties to the aesthetic qualities of this material, while also eliminating waste.
For the door inserts and dashboard strip, the assembly process was optimised using innovative solutions requiring no welding or gluing, for easier recycling.
As part of a ‘Shy Tech’ approach, the conventional controls are replaced with buttons concealed under the surface (window lifts, central screen), for a more durable minimalist design.
Headlights – Forvia Hella
Renault maintains the headlamps developed by Forvia Hella halve their lifecycle CO2 equivalent emissions compared to conventional headlamps. To do this, they use fresnel lenses, which require 80% less material. Optimized design, the use of innovative injection processes, as well as the use of recycled and bio-sourced materials, contribute to half of the reduction in carbon footprint. The manufacture of the product in carbon-neutral factories from the end of 2025 will contribute up to 30%. Finally, the adaptive light intensity control reduces energy consumption by 60% in the city centre.
Tyres – Michelin
Tyres play a crucial role in low-carbon vehicle projects, since they account for around 20% of vehicle energy consumption. On its unveiling at the Paris Motor Show, Emblème was fitted with specially designed and optimised MICHELIN Primacy 215/45-R22 tyres. Optimised for aerodynamic performance, the tyres developed by Michelin push back the limits of rolling resistance still further, it is claimed. The Slimline has a rolling resistance of4.5 kg/T, with no trade-off on other aspects of performance, compared with 5.5 kg/T for conventional tyres. Based on LCA, this innovation will improve vehicle durability by 55% and reduce the carbon footprint of the tyres by over 40% by 2035.
Hydrogen tank – OP Mobility
To reduce the vehicle’s weight and carbon footprint, the hydrogen tank is made from carbon fibre using low-carbon energy.
Electronic components – ST Microelectronics
Emblème uses ST’s SiC (silicon carbide) technology for the traction inverter, to convert energy from the EV battery to drive the motor. SiC is an innovative technology that complements silicon in power electronics, essential for managing energy flows, autonomy, and vehicle charging. It is more robust than silicon for high-performance EVs and more environmentally friendly, as it reduces energy losses, handles higher power and voltage levels, and offers better energy and thermal performance. By 2030 ST aims to reduce CO2 equivalent emissions of the traction inverter by ~80% over its lifetime, compared to a 2018 Renault Megane. This reduction is based on ST’s carbon neutrality roadmap, covering all direct and indirect emissions and product transportation, and achieving 100% renewable electricity sourcing by 2027. Innovative semiconductor designs will also cut CO2 equivalent emissions in production and use phases, it is claimed.
Complete windscreen wiper system – Valeo
Valeo has developed an innovative wiper system comprising a brushless motor, Nanojet Aquablade wipers and 3D printed polymer parts, for a total reduction in CO2 equivalent emissions around 60%. The Nanojet Aquablade is made from recycled materials and uses a technology with a larger number of spray holes along its blade, which is of a smaller diameter than the conventional AquaBlade™ achieving 60% reduction in CO2eq emissions. This design improves cleaning performance while requiring fewer cycles to maintain the same wiping quality. As a result, it uses less cleaning solution, and therefore works with a smaller, lighter tank.
3D printed polymer parts reduce CO2eq emissions by half. Finally, the brushless motor is lighter and more efficient, reducing CO2 eq emissions by 70%.
Electric battery – Verkor
Designed by Verkor, with a production projection towards 2035, the Renault Emblème electric battery displays a 72% reduction in carbon emissions compared to an equivalent traditional battery. This performance is achieved through optimized manufacturing processes, a factory powered by low-carbon electricity, local suppliers, and optimized recycling of waste and end-of-life batteries.