The need for car radiators to be both efficient as well as tough – particularly in racing applications – has led one UK company to develop a new method of manufacture. Mark Wilkinson reports.
On the track at 200mph, the Formula 1 car’s exposed surfaces face all sorts of hazards from small stones and grit thrown up by other cars’ wheels, let alone the occasional prang. In these harsh conditions, one of the most vulnerable components is the radiator – especially as it also needs an uninterrupted flow of air with which to dissipate heat from the engine and other systems.
Enter Applied Cooling Technology (ACT), a Midlands-based manufacturer of cooling devices for industrial applications. Managing director David Pierce devised and patented a unique method of manufacturing finned cooling devices. Traditionally, cooling fins have been attached to radiators and heat exchangers by brazing or welding – both very effective, but sadly, heat-dependent methods. The heat applied during welding can change the metallic structure of the (typically aluminium) radiator tubing, usually weakening the finished item. Therefore, though the original tube may be very strong, the heat used during fin attachment can have a softening effect.
David Pierce explains that ACT’s new ‘ElfinMaster’ machine uses a linear motor to ‘swage’ fins onto the coolant-carrying tubes (made from aluminium, stainless steel or titanium) – sliding and pressing the fins into place under high pressure to achieve a complete interference fit. This robust attachment is achieved without heat, resulting in an extremely strong radiator. ACT is currently developing aluminium-finned titanium tube radiators for possible motor racing applications.
One of the most graphic tests of these prototype radiators is their ability to withstand a shotgun blast. Says Pierce: “At a 50ft range, the shotgun blows through a standard aluminium tube, whereas our radiator tubes suffer no more than a slight dent.”
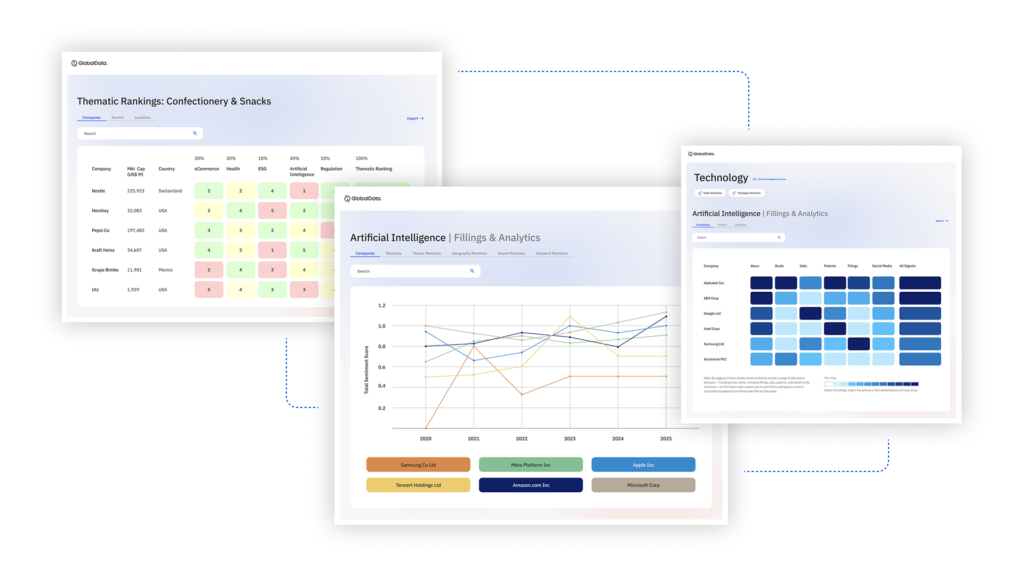
US Tariffs are shifting - will you react or anticipate?
Don’t let policy changes catch you off guard. Stay proactive with real-time data and expert analysis.
By GlobalDataIn order to maximise the cooling potential, ACT also uses vortex generator know-how – enabled by carefully shaping and curving the radiator fins – to generate vortices in the air as it passes over the radiator, resulting in cooling efficiency improvements of up to 25 percent. The linear motor’s digital controllability also provides another advantage – fin placement to within a +/- 5-micron tolerance – which enables the supply of perfectly thermally-matched replacement radiators if units are damaged during race testing.
Since it began its work on automotive applications, ACT has found that its unique advantages of high efficiency, light weight and compactness – along with genuine bullet-proof durability – have naturally led to other possibilities. Off-road motorbike radiators, high performance supercharger intercoolers – and, of course, aerospace and defence applications – are all currently being investigated.