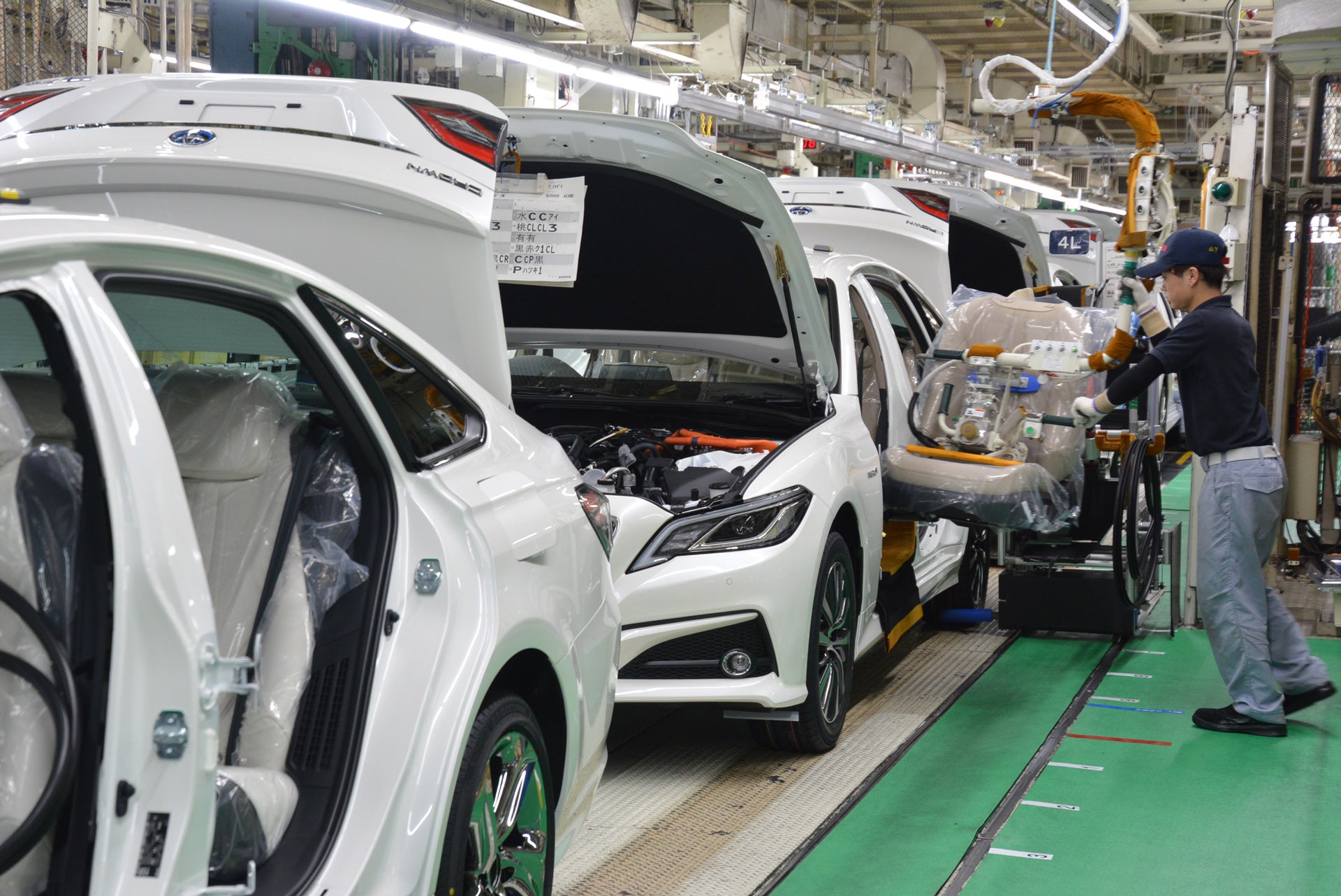
The automotive industry uses a variety of sealants and adhesives within the car manufacturing process. These perform roles that vary from securing pieces together to ensuring seams stay put. One huge benefit of utilising sealants is cost and emissions reduction when compared to alternatives in some applications – such as welding, which is a relatively costly and emissions-heavy process.
Discover B2B Marketing That Performs
Combine business intelligence and editorial excellence to reach engaged professionals across 36 leading media platforms.
Sunstar Engineering works with automotive manufacturers worldwide. Its operations include a factory specialising in innovative lightweighting sealants and adhesives for the automotive market including special adhesives for electronic components. It says these components are helping automotive manufacturers create lighter, more durable, and efficient vehicles.
We spoke to Nicholas Huff, manager, new technology group, Sunstar Engineering Americas, and Stephen Howe, senior director, technical operations, Sunstar Engineering Americas, to learn more about the benefits of adhesives as well as to discuss how they work with clients to achieve goals.
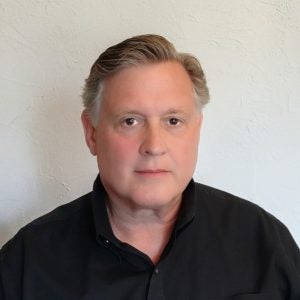
Just Auto (JA): Could you provide some background on the company?
Stephen Howe (SH): Engineering is a division of the general Sunstar company. Sunstar is a diversified company. We have business in oral care, health and beauty, chemicals, and motorcycle parts in construction.
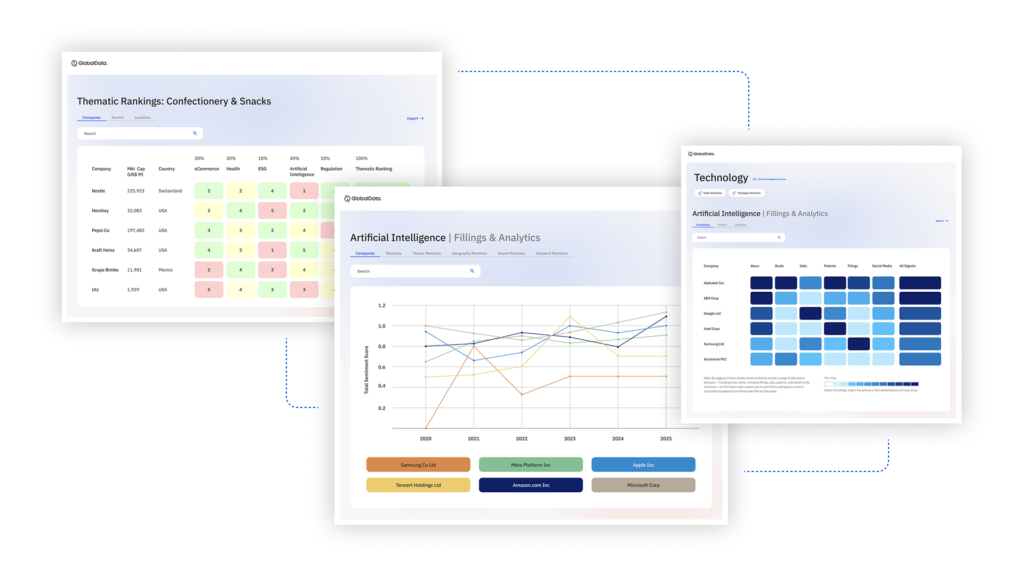
US Tariffs are shifting - will you react or anticipate?
Don’t let policy changes catch you off guard. Stay proactive with real-time data and expert analysis.
By GlobalDataThe chemical part and motorcycle and construction is in Sunstar engineering. We’re about 35 to 40% of the of the business. Nick and I are in Sunstar Engineering Americas; most of our business is in automotive is supplying sealants and adhesives for OEMs. We also provide some materials to Tier 1 suppliers to the OEMs.
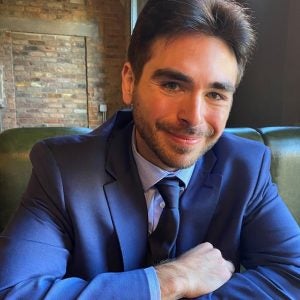
Nicholas Huff (NH): We are a very global company. We have our R&D facilities, sales, and manufacturing here in the US. We have similar set-ups in Europe and we have our Sunstar Engineering European group centred in Germany. We also have a very large group in Japan; our Sensor Engineering Japan group and manufacturing, sales, engineering over there, too. We also have a group in Thailand, and we have some offices in Singapore.
What benefits do adhesives bring to the automotive industry?
NH: You’ll perhaps be surprised to learn that most automobiles now are really glued together, rather than just welded. That trend is increasing and it is being driven by changes in design to vehicles.
Lightweighting is a very critical area right now to improve efficiency and reduce carbon emissions. Increasing the fuel efficiency of vehicles is a big focus and of course, the lighter vehicle, the less energy is required to move it.
Lightweighting is a very critical area right now to improve efficiency and reduce carbon emissions.
Automotive manufacturers are employing many strategies to reduce the weight of their vehicles. It includes making use of alternative substrates. Instead of largely fully steel vehicle structures, there is now significant use of aluminium. But aluminium and steel don’t weld together very well, you have to incorporate adhesives and that’s where our business is certainly growing.
Adhesives also play a role in dampening noise and vibration in a car. As far as road noise is concerned, we can reduce vibration and associated noise with things like mastic adhesives – especially useful with structural pieces that have damping capability. There’s also a comfort aspect there as well, where adhesives can play an important role.
SH: If you go back to the original vehicle manufacturer, adhesives and sealants have always played a significant role it has been increasing. You have a lot of joints in the cars when you’re manufacturing cars. If you look on the inside of your car door, there’s an inner and outer section, for example. If you look closer at your vehicle body, you’ll see the same thing. There are a lot of seams, and those seams provide an area where moisture and salt can get in and cause corrosion.
A really big part of the role of the sealants we have, alongside adhesives, is to prevent corrosion. They also play a big role in being able to use dissimilar materials because you can’t really weld them all together. They also aid in distributing stresses. A problem with welds is they focus the stresses right on those weld points. With time you get a phenomenon called fatiguing. By distributing those stresses, you can prevent that fatiguing process.
It also decreases the cost to the car manufacturer as well, and aids in making assembling much more efficient.
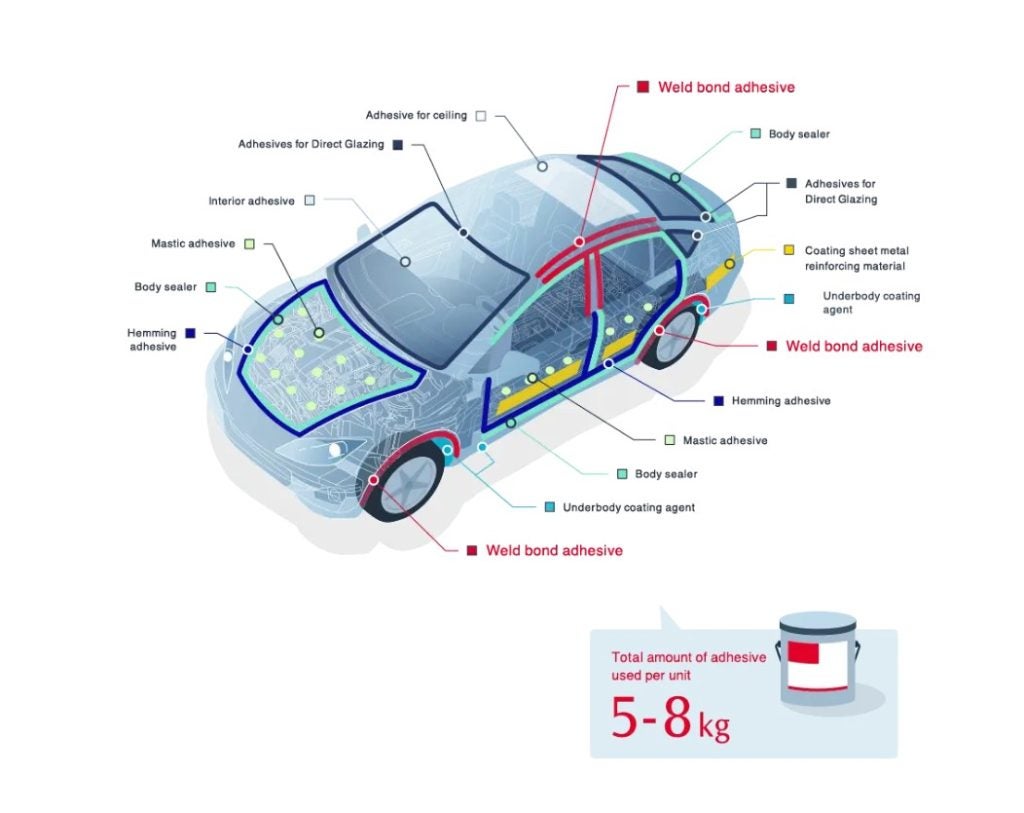
How do adhesives and sealants assist in reducing carbon emissions and low energy manufacturing?
NH: In the automotive manufacturing process, depending on the design of the factory, up to 90% of the energy consumption in the factory comes from the weld and paint shop processes.
The process goes from the stamping area where metal is cut and then stamped into shapes. The shapes are welded and glued together. Then it goes through an anti-corrosion bath where a coating is applied onto the vehicle structure. That coating has to be cured, and to cure it, it goes through a series of ovens; those ovens consume a lot of energy. Then after that, it goes to the paint shop where sealants and other coatings are applied in addition to the paint. Then the body must go through yet another series of ovens and so there is a tremendous amount of energy that’s used in those ovens, which cost the OEMs quite a lot to use.
These ovens consume a lot of energy and depending on the energy sources, much of it is coming from fossil fuels, so a lot of carbon dioxide is emitted to the atmosphere from that whole process.
To meet all these regulations that have come into place over the past few years to reduce carbon consumption, as well as to reduce energy costs, and reduce the cost of manufacturing, OEMs are looking for ways to turn down those ovens. Or even eliminate those ovens if they can. It’s very important research that we’re doing right now. We’re looking at taking our adhesives, our sealants, and our coatings and being able to cure them at much lower temperatures, or potentially finding ways to cure them without a thermal input at all.
SH: Our OEMs all have targets. Many of them are similar, but there’s differences in the timing of when they want to achieve a lot of these goals. Some of it depends on where they are, of course. Energy is more expensive or more sustainably generated in some areas of the world than in others.
How do you work with OEMS to achieve their goals?
NH: There’s a lot of back and forth that we do between our research groups and the OEM research groups at their design centres. We feel out what their targets are, what their goals are, and then we – as the material experts – provide them with solutions and options.
There’ll be a degree of tailoring of how we put together our material for their applications. This is a process that can take months or even years depending on the project, but that’s how we like to approach those situations. It’s a partnership, it’s a joint development.
SH: The way we like to work with customers, typically they will have specifications, a list of requirements. There are strength requirements, adhesion requirements, there are some application requirements, long-term durability requirements. However, we don’t really know everything from a requirement list.
One of the things that we do is go into the customer’s assembly line and understand the requirements that aren’t written on the specification. In terms of the manufacturing process, if you’re bonding through oily, dirty metal, that is something that has to be considered, and you have to understand exactly what materials the OEM is using and be able to test and design for that.
There’s a whole series of baths that the car will go through – detergents, rinses etc. In some cases, they’ll take a car, and they’ll rotate it through a big bath. Now you can imagine if you have an uncured adhesive, this adhesive has to be fluid enough, with low viscosity, to easily apply at a very high rate, hundreds of millimetres a second application rates. At the same time, you’re effectively sending this thing through a carwash and expect the adhesives to stay in place!
So, understanding the rheological [flow behaviour] performance, and what properties it takes to really withstand the manufacturing process is one of the bigger challenges.
The other thing is the curing. There is a temperature cure, and they want to lower the temperature. But one of the difficult things sometimes to design for is that there are some large variations in the ovens and in the temperatures. So, they will give you a target temperature, but they also want it to able to withstand different heats for longer times, and on top of that they want it to be shelf-stable for six months. There are a lot of unwritten, non-spec items that we have to consider and be able to work through with the OEM.
What do you predict to see growing in the automotive space and when?
NH: I think electrification comes with very specific engineering challenges. How do you make battery packs foolproof and completely safe? There’s a lot of opportunity there because in the manufacturing of the battery packs, there is a lot of adhesive encoding type material.
There are two real big areas emerging: one is for the actual thermal management of the battery packs, to make sure that they stay cool and there’s not a runaway reaction. The other big area is for recyclability, sustainability. We have to think about the end-of-life of these battery packs and how they have to be disassembled. There’s not an easy way to do that right now with the latest generation of battery packs.
I think electrification comes with very specific engineering challenges.
The lifespans are ten years or so, which means battery packs that were made ten years ago were not being assembled the way they are now. Recycling and disassembly can be a dangerous process. We were talking to some research professors at the University of Michigan at their EV technical centre, and they were explaining to us what a dangerous process it is to recycle these large battery packs.
So a big push is for adhesives that can de-bond on demand. You apply some sort of energy, heat or maybe something else that will effectively de-bond the battery. Then you can have a much easier way to disassemble and recycle the various components inside the battery packs. There’s opportunity there.
The biggest thing that we’re focused on right now is low-energy carrying materials. That is a very big high priority for us, as well as providing more adhesive solutions in general.
SH: We are looking at carbon neutrality for the entire chain of the materials we’re presenting. There really aren’t any consistent or agreed upon ways to fully measure carbon neutrality and the carbon targets. So, as we go forward, we’re trying to keep abreast of that.
In terms of our research, and the research of our customers, you will see a lot more use of modelling and simulation. This is an area we’re very interested in. We have a role in terms of standardising how adhesives are tested and how the data from those tests is incorporated into simulations and modelling.